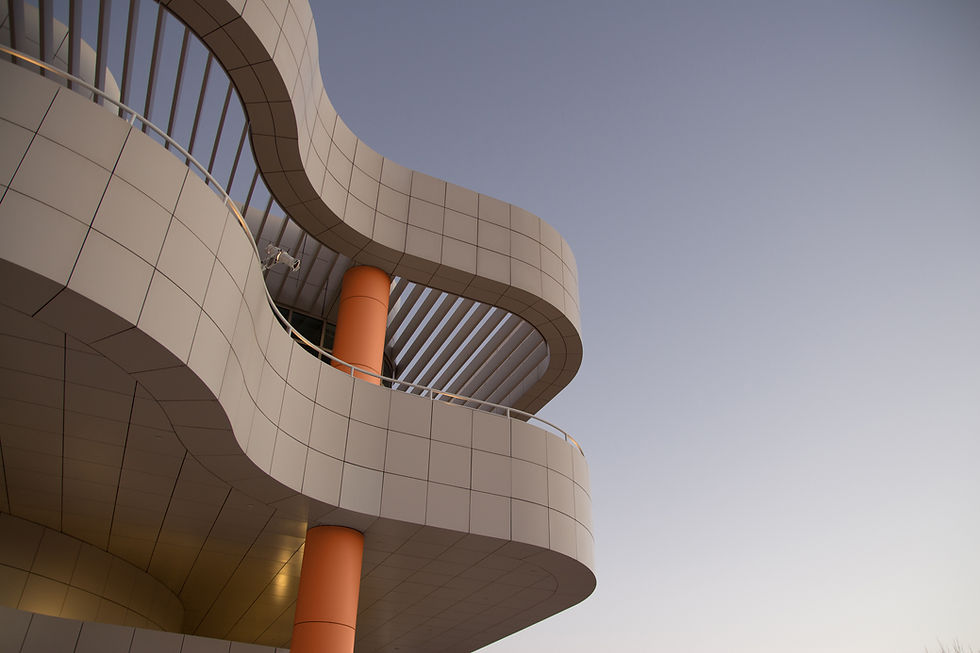
In today’s fast-paced world, businesses are under constant pressure to improve. Whether it’s delivering better customer service, reducing costs, or increasing efficiency, the ability to adapt and improve is crucial for survival. This is where Kaizen comes in — a simple yet powerful concept at the heart of Lean thinking.

What is Kaizen?
Kaizen (pronounced kai-zen) is a Japanese word that means “change for the better” or “continuous improvement.” It’s more than just a tool — it’s a philosophy and mindset that encourages small, incremental improvements every day, by everyone, everywhere.
Kaizen is not about making sweeping changes overnight. Instead, it focuses on identifying small opportunities for improvement and acting on them consistently. Over time, these small changes add up to significant transformation.
Core Principles of Kaizen
The Kaizen philosophy is built on several key principles:
✅ Continuous improvement: Improvement is an ongoing process, not a one-time effort.✅ Respect for people: Everyone’s ideas matter, from frontline workers to executives.✅ Elimination of waste: Focus on removing activities that don’t add value.✅ Standardization: Once improvements are made, they should be standardized to maintain gains.✅ Teamwork and collaboration: Improvement is a collective effort, not a solo task.
How Kaizen Works in Practice
Kaizen can take many forms in organizations, from formal events to daily improvements:
Kaizen events or workshops: Intensive, short-term improvement activities (usually 3–5 days) focused on a specific process or problem.
Daily Kaizen: Small, everyday suggestions and improvements by employees at all levels.
Suggestion systems: Structured ways to capture and implement employee improvement ideas.
Benefits of Kaizen
Organizations that embrace Kaizen experience a range of benefits:
✅ Improved quality and customer satisfaction✅ Reduced waste and lower costs✅ Faster and smoother processes✅ Increased employee engagement and morale✅ Stronger teamwork and communication✅ A resilient, adaptable culture
Steps to Start with Kaizen
Engage your people — Encourage everyone to look for small improvements.
Identify improvement areas — Focus on processes that cause frustration or inefficiency.
Analyze the current state — Use tools like process maps or root cause analysis.
Implement small changes — Pilot improvements on a small scale.
Standardize and share — Lock in successful changes and share learnings across teams.
Repeat the cycle — Keep the momentum going by making continuous improvement part of daily work.
Common Challenges
While Kaizen is simple, organizations often struggle with:
Lack of leadership support
Employee fear of change or blame
Focus on big projects instead of small wins
Failure to sustain improvements over time
Overcoming these challenges requires building a supportive culture, recognizing efforts, and showing quick wins.
Conclusion
Kaizen is more than a method — it’s a mindset that empowers people at all levels to make things better, every day. By embracing Kaizen, organizations can create a culture of improvement that drives long-term success, resilience, and innovation.