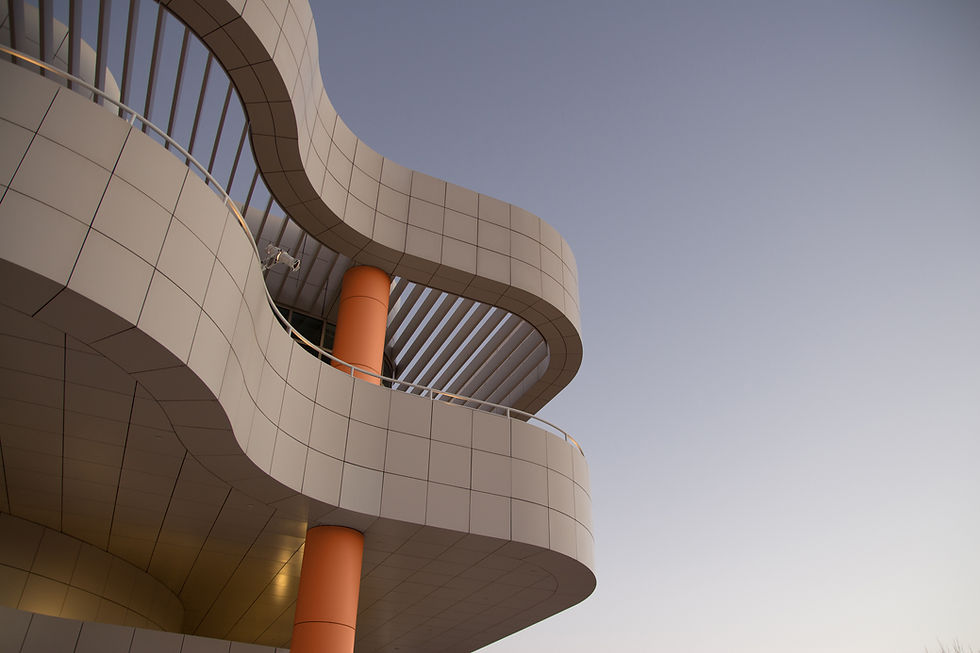
Your handy beginner’s guide to sounding smart in Lean conversations
Suppose you're just starting with Lean. In that case, you’ve probably come across some unfamiliar words — terms like “Kaizen,” “Gemba,” or “Kanban” might sound more like a travel itinerary than a business approach. Don’t worry — you’re not alone!
To help you get comfortable with Lean thinking, here’s a quick breakdown of key Lean terms you’ll hear again and again.

🧹 5S
It is a simple yet powerful method for organizing any workspace. It stands for Sort, Set in order, Shine, Standardize, Sustain. It helps create a clean, safe, and efficient environment where everything has its place.
🛠 Kaizen
A Japanese word means “change for the better” — or continuous improvement. Kaizen is about making minor, incremental daily improvements, often driven by the people doing the work.
👀 Gemba
This means “the real place” in Japanese. In Lean, Gemba refers to where the work happens — whether that’s a factory floor, a hospital ward, or a call center.“Going to the Gemba” means getting out of the office and observing the process firsthand.
🛑 Muda
This term means waste — anything that doesn’t add value for the customer. There are seven types of waste in Lean:
Overproduction
Waiting
Transportation
Overprocessing
Inventory
Motion
Defects
“Skills” is sometimes added as the 8th waste — underused human talent.
🧾 Value Stream
This is the entire set of steps involved in delivering a product or service — from start to finish. A Value Stream Map is a Lean tool used to visualize and analyze this flow, identifying where waste or delays might be hiding.
📊 Kanban
A visual system that shows work in progress. Think of a whiteboard or digital board with columns like “To Do,” “In Progress,” and “Done.”It helps teams manage the flow and avoid overload.
🧮 Takt Time
This is the pace at which products or services need to be completed to meet customer demand. It’s calculated by dividing available time by customer demand. Keeping in sync with takt time helps prevent overproduction or bottlenecks.
🔄 Pull System
Unlike a “push” system (where work is shoved downstream whether needed or not), a pull system means work only moves forward when there's demand. It reduces excess inventory and keeps the flow smooth.
🎯 Root Cause Analysis
The practice of digging beneath the surface of a problem to find out why it’s happening — not just treating symptoms. Tools like the 5 Whys or Fishbone Diagram help here.
🧭 Standard Work
The best-known way to perform a task is documented and shared across the team. It ensures consistency, helps with training, and forms the baseline for future improvements.
Final Thought
Learning Lean doesn’t have to feel like learning a new language (even though some terms are Japanese). Once you understand these key concepts, you'll be better equipped to join improvement conversations, identify waste, and contribute real value to your team.