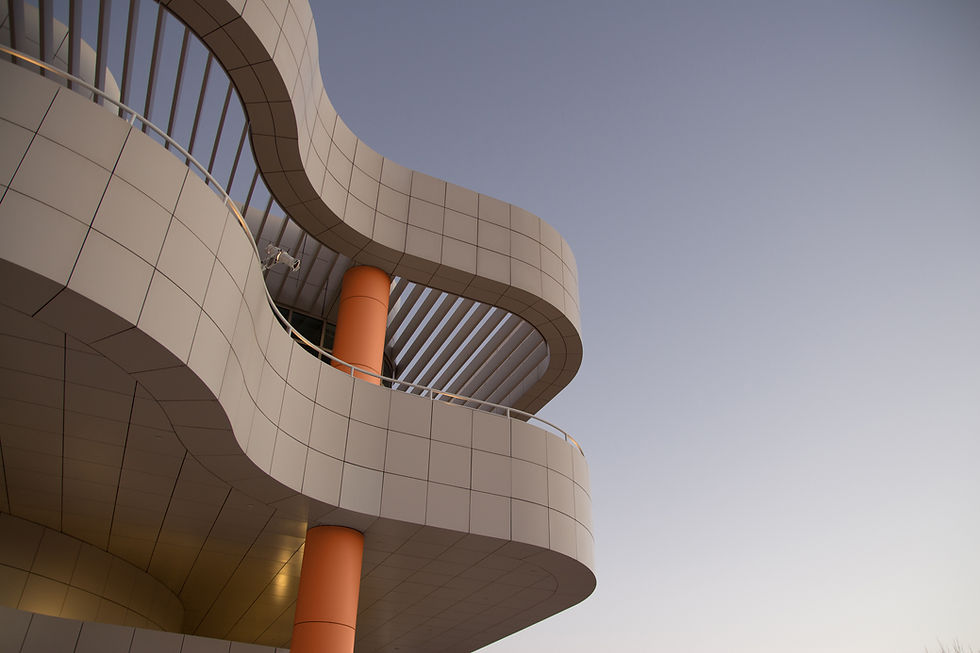
Understanding Lean Thinking
At its core, Lean is about one simple idea: creating more value for customers with fewer resources. Originating in manufacturing, Lean has evolved into a universal approach that applies to every industry—from healthcare and finance to software development and education.
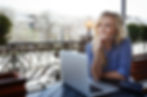
Imagine running a business where everything flows smoothly. Work is done efficiently, customers are happy, and your team isn’t constantly having firefighting problems. That’s what Lean helps you achieve. It gives you the tools and mindset to identify what truly matters, eliminate what doesn’t, and continuously improve how you deliver your products or services.
Lean isn’t just a toolbox. It’s a way of thinking—a cultural approach that emphasizes respect for people, problem-solving, and performance improvement.
A Brief History of Lean
Lean has its roots in post-World War II Japan, where Toyota developed what became known as the Toyota Production System (TPS). Engineers Taiichi Ohno and Shigeo Shingo crafted a new way of working focused on eliminating waste, optimizing flow, and empowering workers.
Instead of mass production with huge inventories, Toyota emphasized just-in-time production, quality at the source, and respect for employees. This approach led to remarkable efficiency and quality improvements, and the rest of the world took notice.
In the 1990s, researchers James Womack, Daniel Jones, and Daniel Roos popularized the term “Lean” in their book The Machine That Changed the World. Since then, Lean has become a cornerstone of modern business improvement across sectors.
Core Concepts of Lean
Lean revolves around five key principles:
1. Value
Start by understanding what the customer actually wants—and is willing to pay for. This is value from the customer's perspective, not what you think is valuable.
2. Value Stream
Map the entire flow of materials and information required to deliver that value. This shows where value is added—and where it’s not.
3. Flow
Once you’ve removed the waste, make the remaining steps flow smoothly without interruptions, delays, or rework.
4. Pull
Instead of pushing work through the system, let customer demand “pull” it. This avoids overproduction and reduces inventory.
5. Perfection
Lean is never “done.” Strive for continuous improvement (Kaizen) to keep making things better.
These principles are simple, but applying them well takes focus, teamwork, and commitment.
Benefits of Lean for Any Organization
No matter what industry you’re in, Lean can help you:
Improve efficiency and reduce delays
Deliver higher-quality products or services
Lower costs by cutting waste
Increase customer satisfaction
Engage employees through problem-solving
Build resilience and adaptability in changing markets
Let’s look at a few examples:
Education:
A university uses Lean to streamline the admissions process, cutting application review time by 40%.
Healthcare:
A hospital maps its patient discharge process and reduces wait times by two hours, improving bed availability and patient experience.
Consulting:
A firm reduces report turnaround time by eliminating unnecessary review steps and automating data collection.
Getting Started with Lean
You don’t need a full Lean department to start. Begin small:
Pick a process - something simple but frustrating (e.g., onboarding, meetings, reporting).
Map it out - use sticky notes to show each step.
Look for waste - identify delays, errors, or unnecessary steps.
Make improvements - remove or streamline wasteful steps.
Get feedback - ask people doing the work what they would change.
Start with curiosity, not perfection. The real power of Lean comes from action.
Summary
Lean is a powerful, flexible way to improve any process. It helps you focus on what matters to the customer, cut out what doesn’t, and keep getting better every day. By embracing Lean thinking, you build not just a more efficient business, but a more engaged and empowered team.