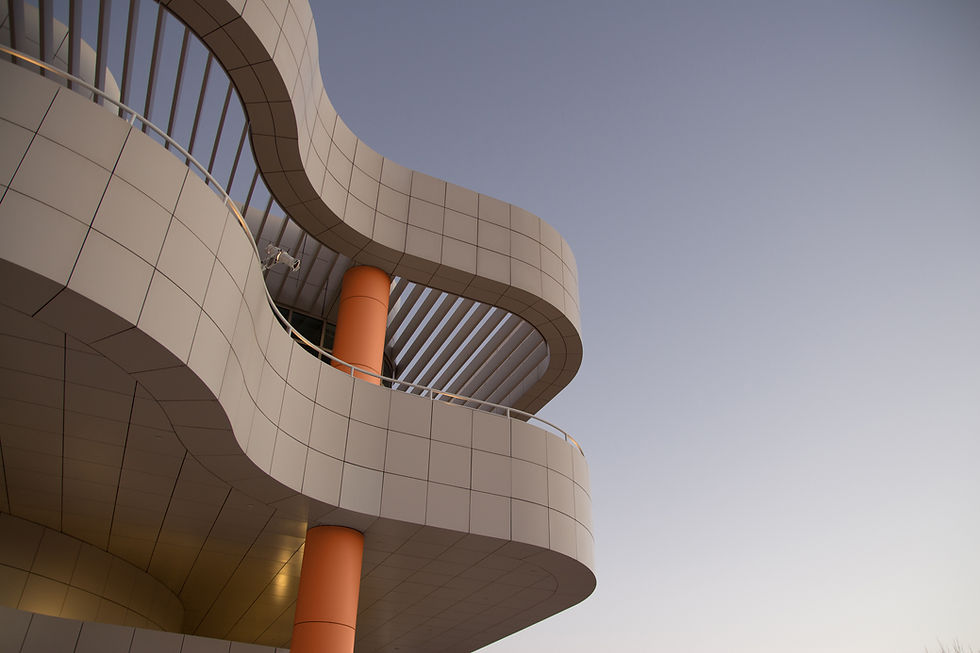
In any business, clarity is power—especially when you're trying to improve a process. Before jumping into root cause analysis or rolling out solutions, it’s vital to understand the landscape of the process itself. That’s where SIPOC comes in.
Whether you're launching a new Lean Six Sigma project or just trying to get a bird’s-eye view of how work flows through your team, a SIPOC diagram offers a structured way to map it all out—from Suppliers to Customers.
What is SIPOC?
SIPOC is an acronym that stands for:
Suppliers – Who provides the inputs?
Inputs – What resources or materials go into the process?
Process – What are the high-level steps that transform inputs into outputs?
Outputs – What comes out of the process?
Customers – Who receives the outputs?
This tool is most commonly used in the Define phase of the DMAIC methodology, but it’s powerful enough to stand alone as a process clarity tool.
Why Use a SIPOC Diagram?
SIPOC brings alignment to teams by answering essential questions like:
Who is involved in the process?
What are the key inputs and outputs?
What are we trying to improve—and for whom?
It’s especially helpful when:
A process spans multiple departments or stakeholders
There’s confusion about roles or responsibilities
You're onboarding new team members or launching process improvement efforts
How to Build a SIPOC Diagram (Step-by-Step)
Start with the Process (P)Identify the 4–7 high-level steps that define the process. Keep it simple. You’re not mapping every detail—just the main flow from start to finish.
Identify Outputs (O)What does the process produce? Outputs can be products, reports, services, approvals—anything that results from the process.
Define Customers (C)Who receives or is affected by the outputs? These could be internal stakeholders or external clients.
List Inputs (I)What’s needed to perform the process? Think data, raw materials, tools, or documents.
Identify Suppliers (S)Who provides the inputs? These might be external vendors or other internal teams.
Example: SIPOC for a Customer Support Ticketing Process
Suppliers | Inputs | Process Steps | Outputs | Customers |
Customers | Support ticket | 1. Receive ticket 2. Triage issue 3. Resolve issue 4. Close ticket | Resolved ticket, Response time report | Customers, Operations manager |
Tips for Success
Facilitate SIPOC with a team, not in isolation. It’s a shared understanding tool.
Use post-it notes or digital whiteboards to encourage interaction and iterative thinking.
Keep it at a high level—don’t get bogged down in subprocesses.
In his October 2024 article, Adebayo Olanrewaju emphasizes the strategic role of SIPOC analysis in Lean Six Sigma and continuous improvement initiatives and shares best practices for using SIPOC:
Involve Cross-Functional Teams: Gather insights from different departments, including suppliers, process owners, and customers, to ensure a comprehensive view of the process.
Focus on the Big Picture: Keep the process steps high-level to avoid unnecessary complexity. The SIPOC diagram is meant to give an overview, not a detailed map.
Review and Update Regularly: SIPOC diagrams should be living documents that are revisited and updated as processes evolve or new data becomes available.
Integrate SIPOC with Other Tools: Use SIPOC in conjunction with other process improvement tools, such as value stream mapping, cause-and-effect diagrams, and control charts, to gain deeper insights.
When to Use SIPOC
At the start of a Lean Six Sigma project
During onboarding of process owners
When preparing for Value Stream Mapping
To communicate with leadership or cross-functional teams
SIPOC’s True Value
SIPOC isn’t just a documentation exercise—it’s a strategic clarity tool. It gets everyone on the same page quickly and provides a solid foundation for diagnosing problems and designing solutions.
By starting with SIPOC, you build a shared lens on how value flows in your organization—and that’s the first step toward real, sustainable improvement.
References
American Society for Quality (ASQ). “SIPOC Diagram.” https://asq.org
Olanrewaju, A. (2024, October 13). SIPOC Analysis in Continuous Improvement. Olanab Consulting Ltd. Retrieved from [https://www.linkedin.com/pulse/sipoc-analysis-continuous-improvement-adebayo-b7frf]