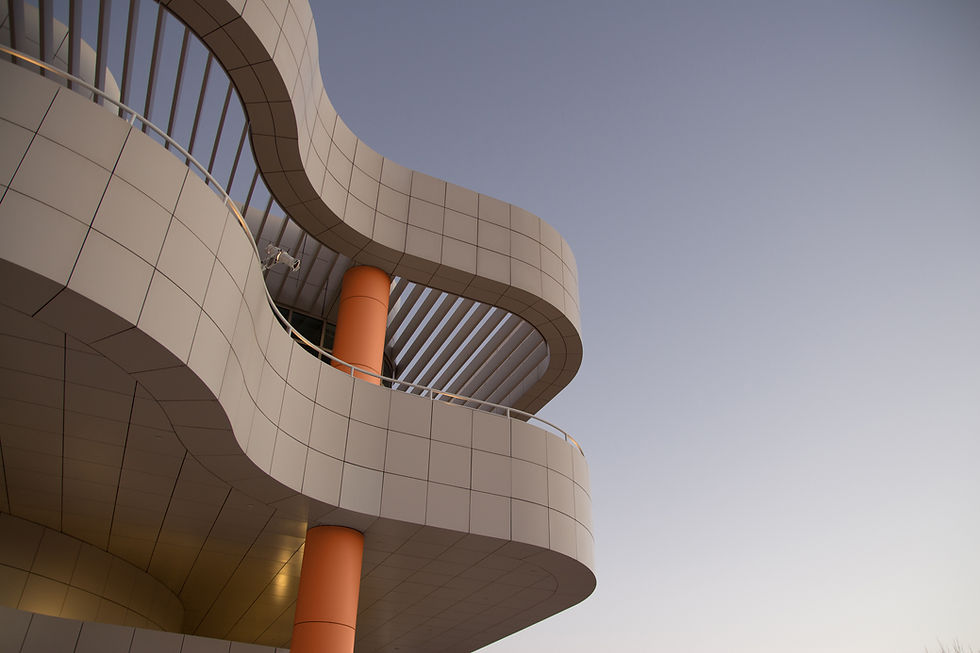
Spotting Bottlenecks and Constraints in Your Value Stream: Why They Matter and What to Do About Them
Jul 12
3 min read
1
4
In any process—whether it's manufacturing, healthcare, software delivery, or service operations—flow is everything. Smooth flow means faster turnaround, happier customers, and better use of resources. But flow is often interrupted by bottlenecks and constraints—the hidden culprits behind delays, defects, and inefficiency.
Understanding how to spot and address these trouble spots is a key skill in Lean thinking and Value Stream Mapping (VSM). Let’s break it down.
🚧 What Is a Bottleneck?
A bottleneck is any step in a process that limits the overall flow of the value stream. Think of it like a narrow bridge on a busy highway—no matter how fast cars move before or after, traffic slows at that point.
Common bottlenecks include:
A step with longer cycle time than others
A department with backlogs or queues
A machine or person that's always overbooked
A quality checkpoint causing rework or delays
🔒 What Is a Constraint?
While bottlenecks are temporary or specific to a process, constraints are more fundamental limitations that cap the performance of the whole system.
Examples of constraints:
Lack of trained staff or specialized equipment
Systemic issues like outdated IT systems
Rigid policies or regulations
Supplier lead times or capacity limits
Key Difference: All constraints are bottlenecks, but not all bottlenecks are system-level constraints.
🔍 How to Identify Bottlenecks in a Value Stream
When mapping a value stream, you want to visualize how work flows from start to finish. Then, look for signs of disruption:
1. Compare Process Times and Takt Time
Takt Time = Available Time / Customer Demand
Identify which steps take longer than takt—they can’t keep up with demand.
2. Look for Inventory Piles or Queues
Excess work-in-progress (WIP) piling up before a process step is a red flag.
A step with frequent backlogs or waiting time is likely a bottleneck.
3. Ask the Team
The people doing the work often know where things get stuck.
Ask: “Which part of the process slows you down the most?” or “Where do you wait most often?”
4. Analyze Process Metrics
Cycle time, lead time, throughput, downtime, first-pass yield—all provide clues.
Use tools like control charts or Pareto analysis to spot variations.
5. Walk the Gemba
Observing the process in real time (Gemba Walks) helps you see delays, waiting, or rework firsthand.
💥 The Impact of Bottlenecks and Constraints
Unchecked bottlenecks can cause:
Delays and longer lead times
Reduced capacity and missed customer deadlines
Higher costs due to overtime, expedited shipping, or rework
Lower employee morale due to overburdening or frustration
Customer dissatisfaction due to inconsistent delivery or quality
Constraints, being systemic, can impact everything downstream and may require strategic investment to resolve.
✅ How to Deal with Bottlenecks
Eliminate Non-Value-Added Work (Waste)
Use Lean tools like the 8 Wastes (TIMWOODS) to simplify and streamline.
Balance the Workload
Apply line balancing to ensure each step has a similar cycle time.
Shift tasks or cross-train employees to spread the load.
Increase Capacity at the Bottleneck
Add staff, equipment, or technology at the constraint.
Automate repetitive tasks where possible.
Implement Pull Systems and Kanban
Prevent upstream overproduction and limit WIP.
Run Kaizen Events
Focused improvement workshops can help fix or redesign the bottleneck step.
Apply Theory of Constraints (TOC)
Identify the system’s constraint, exploit it, subordinate everything else to it, elevate it, and repeat.
🔁 Monitor, Re-Map, and Improve
Bottlenecks shift as processes improve. That’s why continuous improvement is key. After making changes:
Re-map the value stream
Track performance metrics
Conduct regular Gemba walks
Get feedback from teams and customers
🧭 Final Thought
Every value stream has a weakest link—and that’s where your improvement efforts should start. By identifying bottlenecks and constraints early, you can target your Lean and Six Sigma strategies where they’ll have the most impact.
Remember, improving flow is not about speeding up every step—it’s about removing the friction that holds the entire process back.