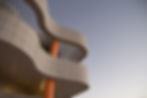
Value Stream Mapping - Designing the Future State
5 days ago
3 min read
0
0
So, you’ve completed the Current State Map. You've walked the process, talked to the people doing the work, captured the numbers, and highlighted the waste. Now comes the exciting part—designing the Future State.
This is where imagination meets logic. The future state is your chance to reimagine the process as it should be—not constrained by today’s inefficiencies or legacy habits. It’s about answering one powerful question:
“How can we deliver more value to the customer with less waste?”
What is a Future State Map?
A Future State Map is a visual depiction of the improved process you want to build. It’s not just a dream; it’s a practical blueprint rooted in Lean principles, grounded in your current-state insights, and designed to move you closer to perfection. It’s the step between identifying problems and implementing real-world change.
But here’s the trick: you can’t just wish your way to a better process. Designing a great future state requires structure, collaboration, and a bit of creative constraint.
Key Design Goals for a Future State
When designing your future state, keep these Lean goals in mind:
Deliver what the customer needs, when they need it (based on takt time)
Eliminate or reduce non-value-added steps
Minimize inventory, waiting, and handoffs
Balance workload and create flow
Use pull instead of push where possible
Simplify and standardize steps
Enable visual controls and problem-solving at the source
5 Steps to Designing the Future State
Let’s walk through the core steps involved in creating your future state map:
1. Revisit Customer Needs and Takt Time
Start by anchoring your design in the voice of the customer. What does the customer really need? What are their expectations for speed, quality, and consistency? This will help you define takt time—the rhythm your process should follow to meet customer demand without overproduction.
2. Redesign the Process Flow for Pull and One-Piece Flow
Look at the current process and ask:
Can we shift from batching to one-piece flow?
Can we move toward pull rather than push?
Where can we eliminate handoffs or combine steps?
This is where waste starts to disappear.
3. Redefine Roles, Responsibilities, and Workload
Lean isn’t about working faster; it’s about working smarter. Redesign roles to match people’s strengths. Standardize steps wherever possible. Balance the workload to prevent bottlenecks or burnout.
Ask:
Who should do what?
Can some tasks be automated or delegated?
Where is there underused capacity?
4. Eliminate Waste and Simplify Decision Points
Next, go through each step and apply a waste lens:
Is this step adding value?
Can it be removed or shortened?
Is the process overly complex?
You might find you can eliminate redundant paperwork, simplify scheduling, or remove approval layers that delay action.
5. Plan for Information and Material Flow
A good future state map shows how materials (or customers) move, but also how information flows. Who gets notified when an appointment is confirmed? How is a service order communicated? Where do delays in information cause bottlenecks?
Design an improved communication flow, and use Lean tools like visual boards, status trackers, or real-time updates to enable this.
Key Elements in a Future State Map
Just like a current state map, your future state should include:
Customer demand and takt time
Process steps (streamlined, rearranged, or removed)
Cycle times, setup times, and inventory levels
Information flow
Pull signals (Kanban, reorder points, triggers)
Improved metrics (lead time, %C/A, etc.)
Keep it visual. Use icons, arrows, and notes to make the process story easy to understand at a glance.
Your future state should be ambitious but realistic. It’s okay if not everything can be changed overnight. Pick improvements that have the highest impact with lowest resistance, and build momentum with early wins.
Also, the future state map is not a “final destination”—it’s just the next best version of the process. As the system improves, your future state today becomes your current state tomorrow—and you start again. That’s the Lean mindset: always improving.