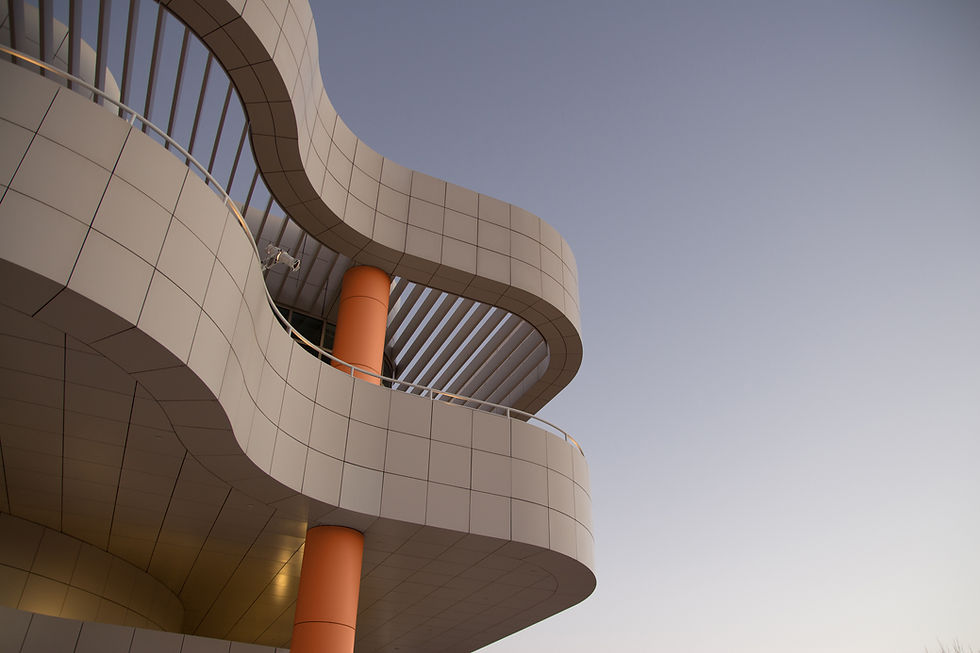
A Lean Walkthrough: Building Your Current and Future State Maps
Jun 30
3 min read
0
3
In the Lean world, mapping is more than just a drawing exercise—it's a strategic tool to visualize, analyze, and improve the way value flows through your organization. At the heart of this technique lies Value Stream Mapping (VSM), which involves creating two key maps: the Current State Map and the Future State Map.
Together, these maps give you the “before” and “after” picture of your processes, helping teams identify inefficiencies and design smarter workflows.
Let’s walk through how to build both maps and use them to drive real improvements.
🏁 Step 1: Define the Process Scope and Objective
Before drawing anything, define the scope of your value stream. This could be:
From customer order to delivery
From inquiry to quotation
From appointment booking to post-service follow-up
Also, align on the goal: Is it to reduce lead time? Improve quality? Increase throughput?
🔍 Tip: Make your goal measurable so you can compare “before” and “after.”
🔍 Step 2: Create the Current State Map
This map captures how things are done today—warts and all. It's not about how the process should work, but how it actually works.
What to Include:
Process steps (with VA/NVA/BVA classification)
Time metrics (cycle time, wait time, lead time)
Inventory levels
Information flow (how orders/instructions travel)
Delays and rework points
How to Build It:
Walk the process (“Gemba”): Observe what’s happening, not just what’s documented.
Interview employees: Understand their challenges and workarounds.
Use post-its or mapping software: Keep it flexible.
Quantify the flow: Capture actual data for time, queue, defects, etc.
Example:
A salon’s Current State Map might show:
Clients calling to book appointments (5 mins)
Staff manually checking availability (delay)
Paper-based logbook entries (2 mins)
Waiting time between booking and service (48 hours)
Manual feedback forms collected post-service
🚩 Step 3: Identify Waste and Opportunities
Use your Current State Map to highlight the 8 Wastes (TIMWOODS):
Transportation
Inventory
Motion
Waiting
Overproduction
Overprocessing
Defects
Skills (underutilized talent)
🔍 Example: Re-entering appointment data into a CRM is overprocessing; waiting for staff to confirm time is a delay.
🎯 Step 4: Create the Future State Map
Now that you’ve visualized the current state, it’s time to reimagine the ideal flow of value. The Future State Map shows what the process will look like after Lean improvements are implemented.
What to Focus On:
Reduce or eliminate non-value-added steps
Simplify handoffs
Digitize or automate where possible
Standardize work
Introduce pull systems (Kanban, scheduling)
Balance workload across teams
Questions to Ask:
Can this step be removed or merged?
Can technology reduce wait time or errors?
Is there a faster or simpler way to deliver value?
Example:
Future State Map for the salon might include:
Online booking system with auto-confirmation
Digital service logs synced to CRM
Post-service feedback captured through SMS link
Reduction in average lead time from 48 hours to 24 hours
📏 Step 5: Develop an Action Plan
Break down the changes required to reach the future state:
What quick wins can be implemented immediately?
What systems/tools need to be built or bought?
Who owns each step of the implementation?
📋 Use a Lean A3 or project tracker to assign owners and timelines.
🔄 Step 6: Implement and Monitor
Turn your map into reality:
Train staff on new processes
Test new systems in pilot mode
Collect metrics (lead time, error rates, NPS) to measure impact
Adjust based on feedback
📊 Use Control Charts or dashboards to track ongoing performance.
💡 Why Both Maps Matter
Current State Map | Future State Map |
Highlights pain points and inefficiencies | Illustrates Lean-enhanced process flow |
Helps build consensus on what’s broken | Inspires alignment on what’s possible |
Serves as a baseline for improvement | Becomes the blueprint for change |
Together, they help teams move from frustration to flow, from firefighting to fixing, and from chaos to clarity.
🧭 Conclusion: Your Roadmap to Lean Transformation
Creating Current and Future State Maps isn’t just a documentation task—it’s a collaborative, strategic effort to make work better. Whether you're tackling waste, delays, or complexity, VSM provides a powerful visual tool to guide your team through change.
📌 Remember: The map is not the territory. It’s a guide—but the journey is driven by people, data, and action.